Applications
With NuPlastiQ’s ability to blend with standard industry resins, the possibilities are endless. Whether it be blown film, durable products, or your own custom process, BioLogiQ’s masterbatch blends are designed to reduce dependence on traditional fossil-based resins, improve the properties of designed products, and reduce microplastic potential at end of life.
Curious about how BioLogiQ can improve your product portfolio and make a real impact for the environment? Speak to a representative today.
BioBlend® Creation
BioBlends® are made by blending BioLogiQ’s iQ® (NuPlastiQ) resin with other conventional fossil-fuel-based resins. BioBlends normally start as Masterbatch pellets containing 50% iQ® (NuPlastiQ) and 50% fossil-fuel resin which are blended on standard compounding equipment. Masterbatch BioBlends are then blended further at the final process to obtain the desired NuPlastiQ content.
Example: for typical film applications, the BioBlend Masterbatch that contains 50% iQ (NuPlastiQ) and 50% virgin LLDPE resin would be fed into the blown film hopper along with an additional 50% LLDPE base resin so that the final BioBlend® content in the finished film would be 25% iQ (NuPlastiQ) and 75% LLDPE. Other ratios are also possible and can be easily established by the appropriate down blending configuration.
BioLogiQ can provide BioBlend® compounded resins directly from our factory in Idaho for trial and production activities. Please contact the factory for a direct discussion of your specific needs.
Reach out to be connected to a BioLogiQ representative to discuss how we can help you achieve your sustainability goals
Blown and Cast Film
BioBlends are a perfect resin for many single-use film applications, including, for example, produce bags, agricultural film, and industrial packaging film.
Films containing BioBlends can be processed on standard film blowing equipment. There are many formulations that are compatible with various grades of LDPE, LLDPE, HDPE, PBAT, PLA, PHA and others. BioBlend/LLDPE films as thin as 2.54 microns (0.1 mil) have been successfully blown.
BioBlends are typically 50/50 masterbatches, meaning they contain 50% of our plant based NuPlastiQ resin and 50% partner resin. Depending on application, BioBlends mixed with additional resin that result in a plant-based ratio between 5% and 40% have the best potential to improve bubble stability, increase strength of blown films, and reduce environmental impact. We have developed the following Film Processing Guide for reference when performing initial product trials.”
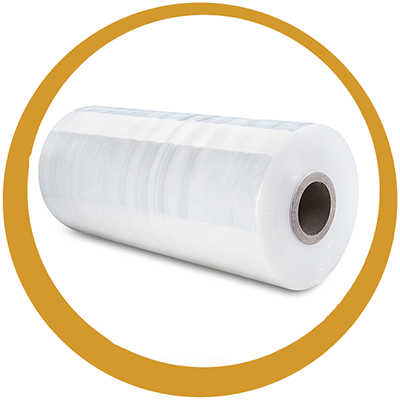
Blow Molding
For a more environmentally friendly profile and end-of-life, Blow Molded Bottles containing a NuPlastiQ BioBlend can be made for health and beauty products (such as lotion bottles). BioBlends masterbatches can also be made from 50% PCR or PIR to further improve your sustainability footprint and increase your recycled content claims. You can achieve a reduction in virgin fossil-fuel content and green-house gases without sacrificing performance.
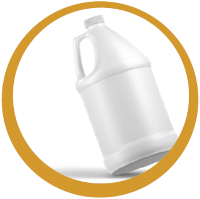
Sheet Extrusion and Thermoforming
Polypropylene, Polystyrene, and PLA are common materials for making thermoformed products such as cups, lids, trays and electronic component packaging. Implementing a NuPlastiQ BioBlend solution adds sustainability, and improves end-of-life impact to these products without sacrificing appearance or performance.
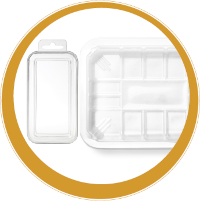
Injection, Compression, and Roto Molding
Both DuraPlantiQ and BioBlends products can be used on standard molding equipment to make a wide variety of products such as cups, cutlery, toys, pallets, or custom-designed plastic parts. Implementing a durable solution with DuraPlantiQ, or a single use application with a BioBlend solution adds sustainability to these products without sacrificing appearance or performance. Compatible with PP, rPP, PE, rPE, ABS, PS, TPE, PBS, PLA, and PHA. .
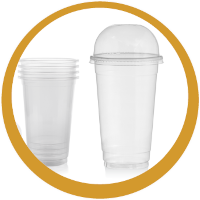
Other Processes
In addition to these standard processes, BioLogiQ will work with you to integrate our technologies into your proprietary processes.
Processes
BioLogiQ’s NuPlastiQ BioPolymer is designed to be used with other thermoplastic resins on standard plastics process equipment. Processing is generally in line with existing processes but may require minor adjustments to process conditions, such as to processing temperatures.
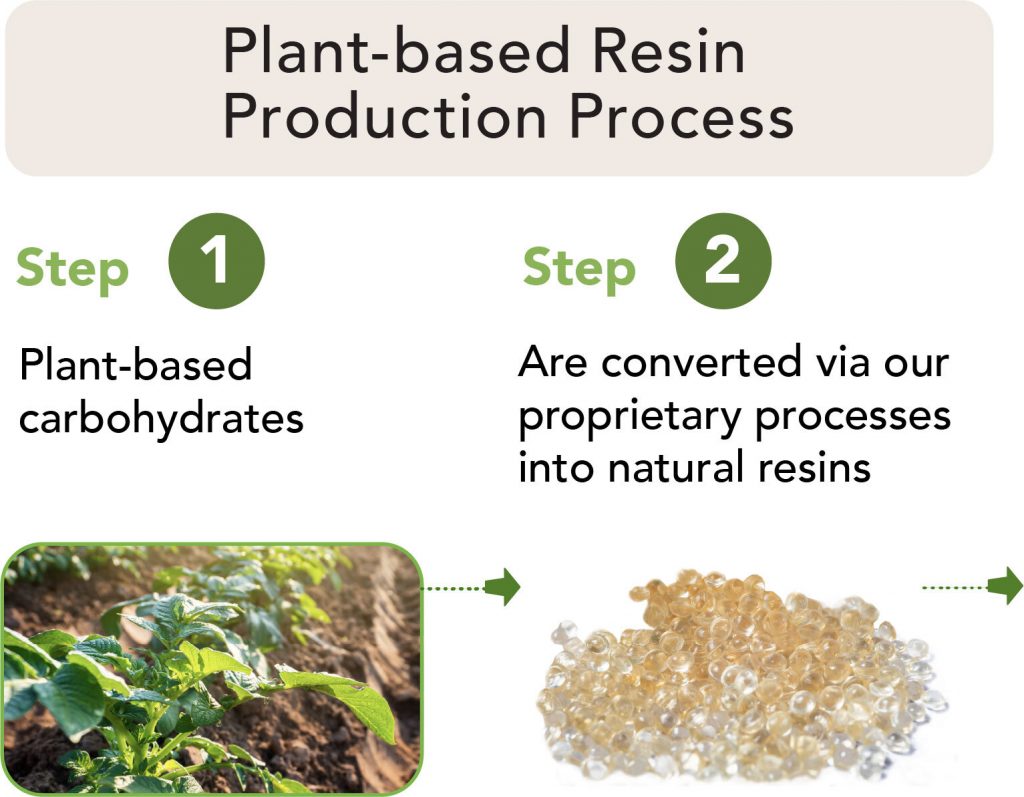
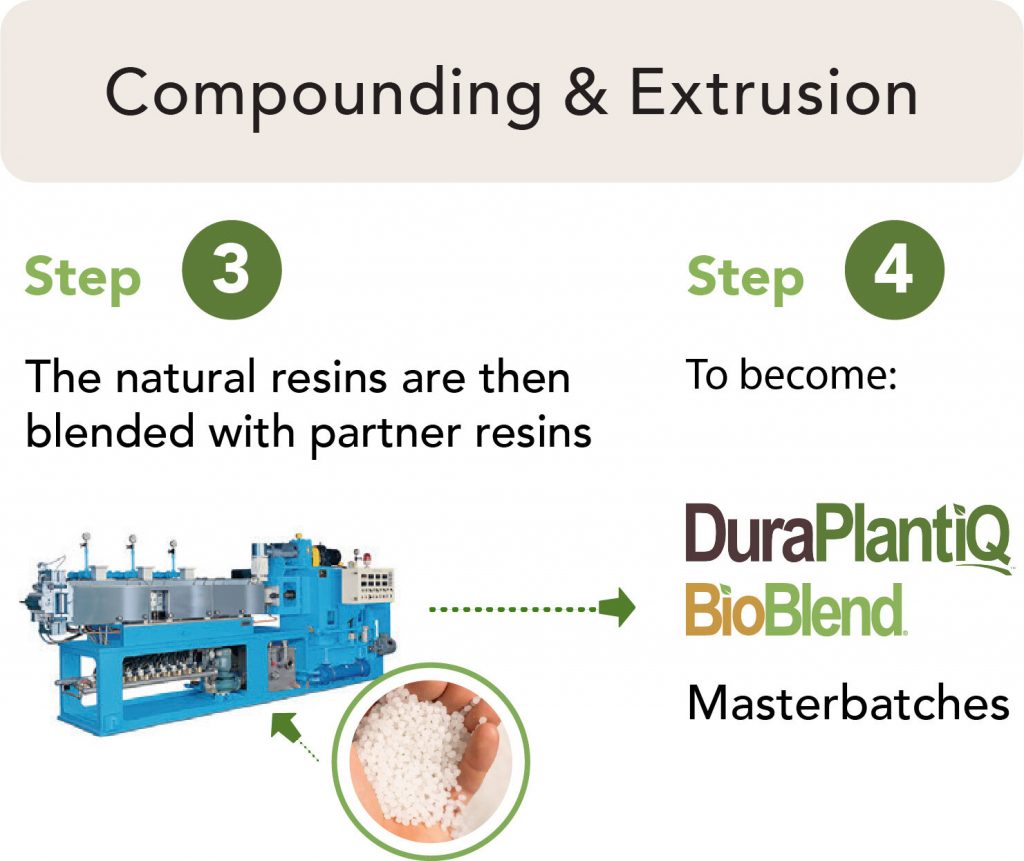
Advantages and Performance
NuPlastiQ acts as a partner resin and can be compounded with legacy plastics to produce BioBlend XP, XD, and BC Resins. These high performing BioBlends are are engineered to provide a more planet friendly solution without sacrificing performance.
Rigid Products: BioBlend XD Resins for rigid products and containers provide improved sustainability metrics related to reduced fossil fuel-based plastic usage and lower greenhouse gas generation while maintaining shelf stability and performance requirements.
- Maintains shelf stability and performance for the intended useful life of the product or package.
- Enables fossil-based material & energy reductions via efficient renewable content addition.
- Reduces potential of persistent microplastics accumulating in the ocean*
- Can reduce resin-related cradle-to-gate global warming potential by 10-40%.
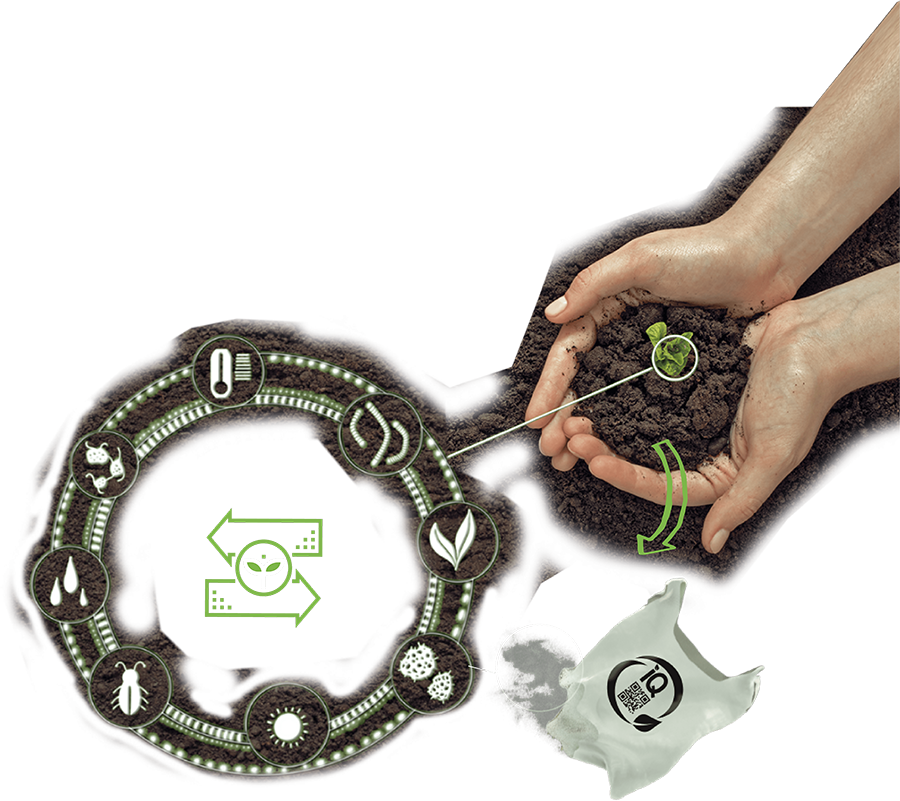
Single Use Flexibles: BioBlend XP High-Performance Resins for packaging will maintain or even increase the overall strength of plastics such as polyethylene, polypropylene, or polystyrene. They can also reduce material use, energy consumption, fossil fuel-based plastics usage, and greenhouse gas (GHG) generation by 10-40%.
- The strength of XP can allow for downgauging.
- XP has an amorphous structure, which makes it easily blended with PE, PP, and PS.
- Using BioBlend XP helps reduce both fossil fuel-based plastic content and greenhouse gas generation.
- Thin films made with BioBlend XP have a softer feel.
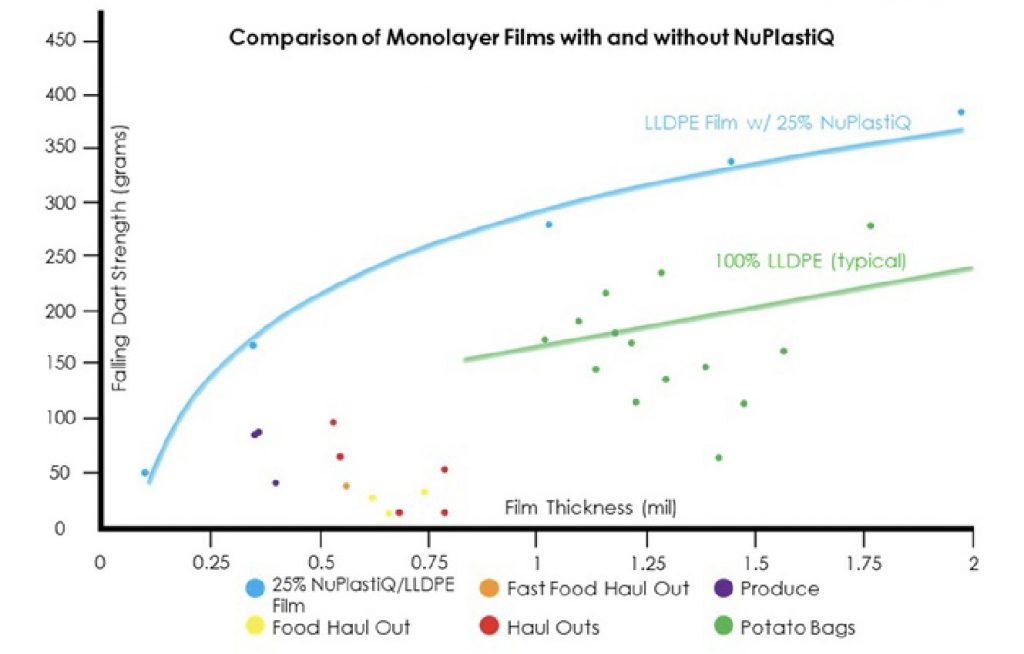
Adding BioLogiQ’s NuPlastiQ to LLDPE or LDPE increases the bubble stability and makes it possible to blow films as thin as .1 mil (2.5 microns)
Bags made with 25% NuPlastiQ and 75% PE that are downgauged by 30% result in up to 50% less fossil fuel being used to make the bags. This, in turn, reduces the amount of conventional non-biodegradable PE that ends up in landfills and the ocean..